Forget huge steel tanks – some scientists want to make chemicals with the help of rocks deep beneath the Earth’s surface. New research shows that ammonia, an essential chemical for fertilizers, can be produced from rocks at ordinary temperatures and pressures below the surface.
The research was published today in Joule, and MIT Technology Review can exclusively report that a new company, called Addis Energy, has been founded to commercialize the process.
Ammonia is used in most fertilizers and is a vital part of our modern food system. It can also be applied as a green fuel in sectors such as transoceanic shipping. The problem is that the current processes used to produce ammonia require a lot of energy and produce large amounts of greenhouse gases that cause climate change – more than 1% of the global total. The new study found that the planet’s internal conditions can be used to produce ammonia in a much cleaner process.
“The Earth could be a chemical production factory,” says Iwnetim Abate, a professor at MIT and author of the new study.
This idea could represent a major shift for the chemical industry, which currently relies on huge facilities that run reactions at extremely high temperatures and pressures to produce ammonia.
The main ingredients for generating ammonia are nitrogen and hydrogen sources. Currently, much of the focus on cleaner production methods is on finding new ways to produce hydrogen, since this chemical makes up most of ammonia’s climate footprint, says Patrick Molloy, director of the nonprofit research agency Rocky Mountain Institute.
Recently, researchers and companies have located natural hydrogen deposits underground. Iron-rich rocks tend to drive reactions that produce the gas, and these natural deposits could provide a low-cost, low-emission source of hydrogen.
Although geological hydrogen is still in its infancy as an industry, some researchers hope to help the process by encouraging manufacturing underground. With the right rocks, heat and a catalyst, it is possible to produce the gas cheaply and without emitting large amounts of climate pollution.
However, hydrogen can be difficult to transport. In that sense, Abate was interested in going a step further by letting underground conditions do the heavy lifting of fueling the chemical reactions that turn hydrogen and nitrogen into ammonia. “When you dig, you get heat and pressure for free,” he says.
To test how this could work, Abate and his team crushed iron-rich minerals and added nitrates (a source of nitrogen), water (a source of hydrogen), and a catalyst to aid the reactions in a small reactor in the laboratory. They discovered that even at relatively low temperatures and pressures, they were able to produce ammonia in a matter of hours. If the process were scaled up, researchers estimate, one well could produce 40,000 kilograms of ammonia per day.
Although reactions tend to be faster at high temperature and pressure, researchers found that ammonia production could be an economically viable process even at 130°C (266°F) and just over two atmospheres of pressure. These conditions would be accessible at depths achievable with existing drilling technology.
Even though the reactions work in the laboratory, there is still much work to be done to determine if, and how, the process can actually happen in the field. One thing the team will need to figure out is how to keep the reactions going, because in the reaction that forms ammonia, the surface of the iron-rich rocks will be oxidized, leaving them in a state where they can no longer react. But Abate says the team is working to control the thickness of the unusable rock layer and its composition so that chemical reactions can continue.
To commercialize this work, Abate is co-founding a company called Addis Energy with $4.25 million in pre-seed funding from investors including Engine Ventures. Its co-founders include Michael Alexander and Charlie Mitchell (who previously worked in the oil and gas sector) and Yet-Ming Chiang, an MIT professor and serial entrepreneur. The company will work on increasing the scale of the research, including searching for potential locations with geological conditions to produce ammonia underground.
The good news for scale-up efforts is that much of the necessary technology already exists in oil and gas operations, says Alexander, CEO of Addis. A system deployed in the field will involve drilling, pumping fluid into the ground and extracting other fluids from below the surface, all very common operations in this sector. “There is new chemistry that is involved in an oil and gas package,” he says.
The team will also work on refining process cost estimates and gaining a better understanding of safety and sustainability, says Abate. Ammonia is a toxic industrial chemical, but it’s common enough that there are established procedures for handling, storing and transporting it, says RMI’s Molloy.
Judging by researchers’ initial estimates, ammonia produced using this method could cost as much as $0.55 per kilogram. That’s more than fossil fuel-produced ammonia currently ($0.40/kg), but the technique would likely be cheaper than other low-emissions methods. Process adjustments, including using nitrogen from the air instead of nitrates, could help reduce costs further, down to $0.20/kg.
New approaches to ammonia manufacturing could be crucial to climate efforts. “It’s an essential chemical for our way of life,” says Karthish Manthiram, a Caltech professor who studies electrochemistry, including alternative methods of generating ammonia.
The team’s research appears to have been designed with scalability in mind from the start. Furthermore, using the Earth itself as a reactor is the kind of thinking needed to accelerate the long-term journey of sustainable chemical production, adds Manthiram.
While the company focuses on scale-up efforts, there is still much work to be done by Abate and other labs to understand what is happening during reactions at the atomic level, especially at the interface between the rocks and the reaction fluid.
Lab research is exciting, but it’s just the first step, says the MIT professor. The next is to see if this actually works outside of a controlled environment.
( fonte: MIT Technology Review)
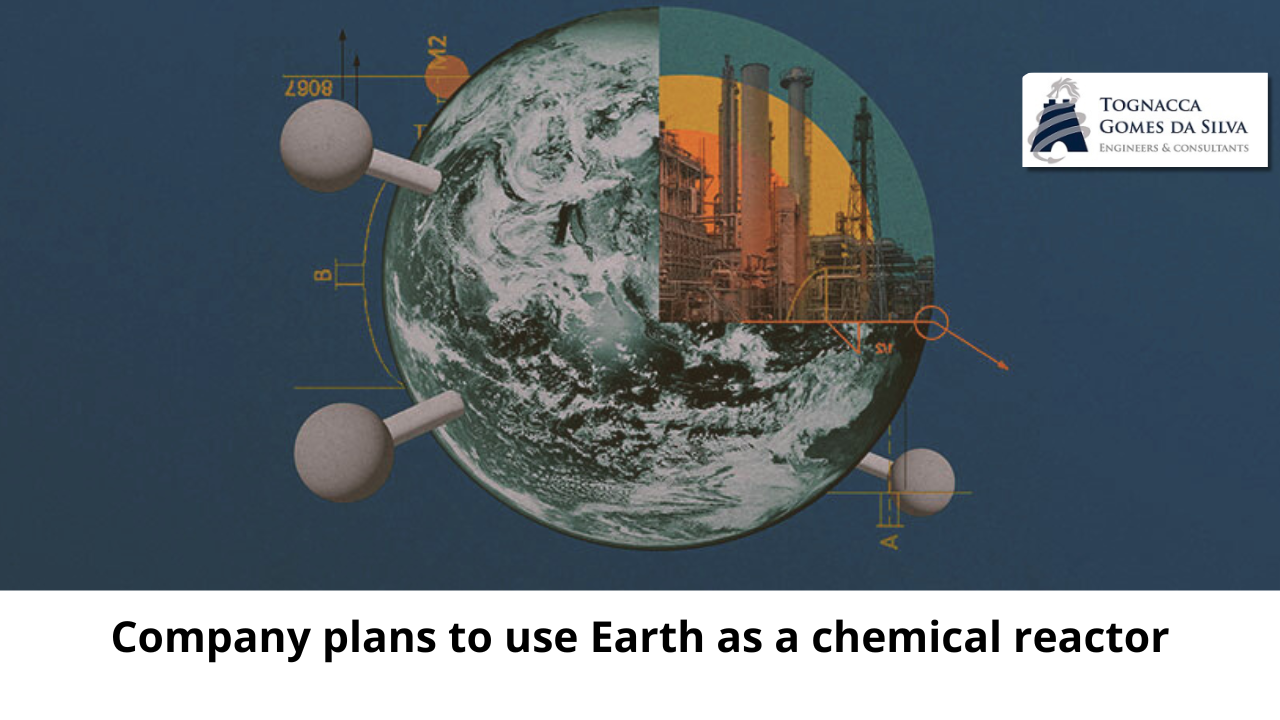